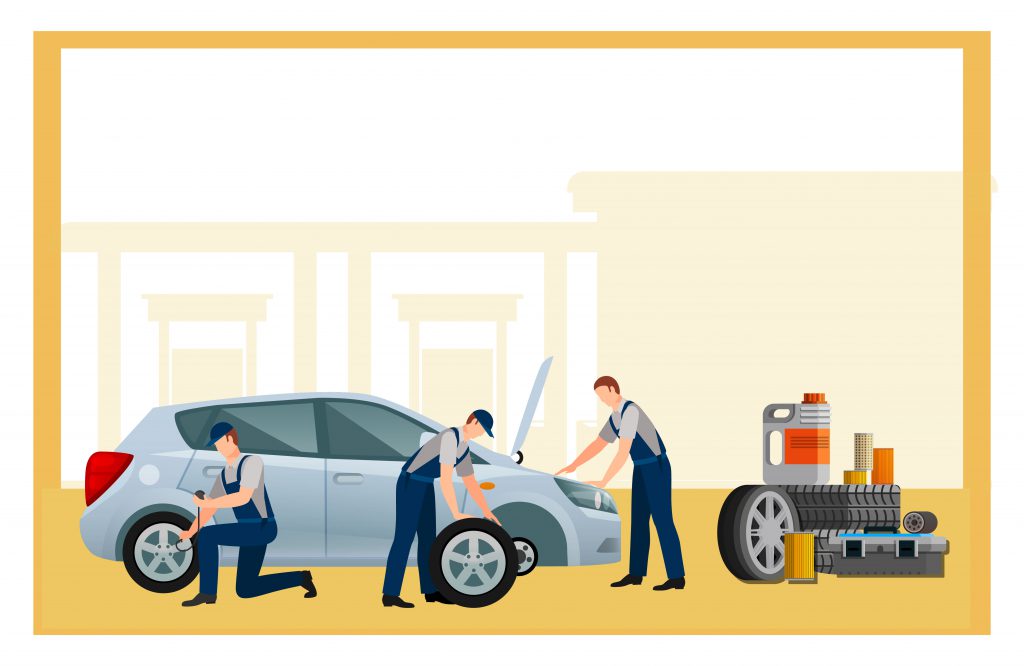
Digitizing Supply Chain: Lubricants and Automotive Supplies Industry
Table of Contents
Lubricants and the entire oil and gas industry in general are in the middle rankings in the digitization level according to the Industry Digitalization Index. However, this digital transformation is mostly only for labor and manufacturing. In terms of digitizing distribution and logistics, the lubricant industry is still lagging behind.
Digitalization in distribution and logistics is very important in streamlining the process of getting products to the market while also minimizing the risk of counterfeit goods.
Pain Points for Lubricants Industry and Automotive Supplies
Building customer trust in the Indonesian market is not easy. Therefore, when a product is counterfeited, the stakes are high, because it damages not only the company’s image but also its profitability.
In addition, with the long supply chain for the automotive material industry, there are also several other problems that the industry often faces:
- Lack of data transparency
- Limited market demand data and product information
- Slow transfer of information from different layers of the supply chain
- Suboptimal operational costs
4 Key Points Why The Lubricant Industry Should Start Digitizing
1. Transparency in distribution with track and trace
Pain points:
With a manual system, companies find it difficult to know where their product is, in which warehouse or at which project location, because there is no system integration with the distributor’s warehouses and retailers. This data is important to know in order to obtain an accurate inventory level to anticipate market demand, optimize inventory costs, and determine time to market. Especially for the lubricant industry in Indonesia, digitizing product identities is very important because lubricants are more prone to product counterfeiting.
Solution:
The application of Quick Response (QR) Codes technology to the packaging of each lubricant bottle as a unique digital identity. After the QR codes are scanned, the system will start tracking product movements (track and trace) starting from the Principal’s warehouse, trucks, distributor warehouses, salesmen couriers, until finally arriving at the store. QR codes can be placed directly on the product packaging or on the box/pallet. A fake product can be detected if there is an unregistered or duplicated QR code circulating on the market.
Read more: Revolutionary Warehouse Management System: A New Way to Identify Products
Benefits:
The unique identity in each bottle of lubricant helps the Principal to prevent counterfeiting and cross-border transactions. In addition to real-time product monitoring, track and trace technology also optimizes production planning because the recording of stock items in warehouses, sell-in and sell-out is done automatically and in real-time.
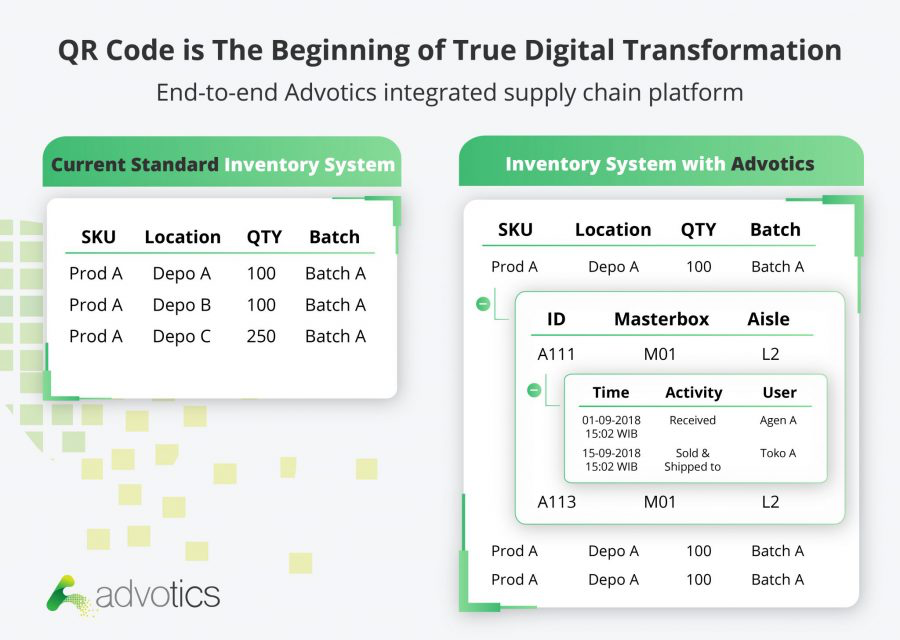
2. Strengthen relationships with Product Advocates
Pain points:
Unlike other products on the market, automotive product specifications are more complex, especially for nontechnical buyers. Therefore, purchasing products such as lubricants and tires requires further product explanation from someone who is trusted in the industry to encourage consumers to buy these products, for example a mechanic in an automotive workshop.
As most of them operate individually, it is often difficult for principal companies to track their sales figures and performance.
So far, to strengthen relations with mechanics, companies have created a special loyalty program to provide incentives so that mechanics are more enthusiastic about selling their products over the competitors. However, because the process is still manual, it’s sometimes difficult for principals to control the distribution of prizes, while for mechanics it’s also difficult to monitor their own collected data points.
Solution:
Companies can start using mobile-based digital applications for loyalty programs. The mechanic can scan the product QR code with every purchase on the loyalty program application to get incentives.
Benefits:
Mechanics can redeem their loyalty points for electronic vouchers, prepaid mobile vouchers, right from their own app. Meanwhile, companies can easily manage, control, and monitor various promotional campaigns in the loyalty program at the same time.
Read more: Loyalty Program for Product Advocates
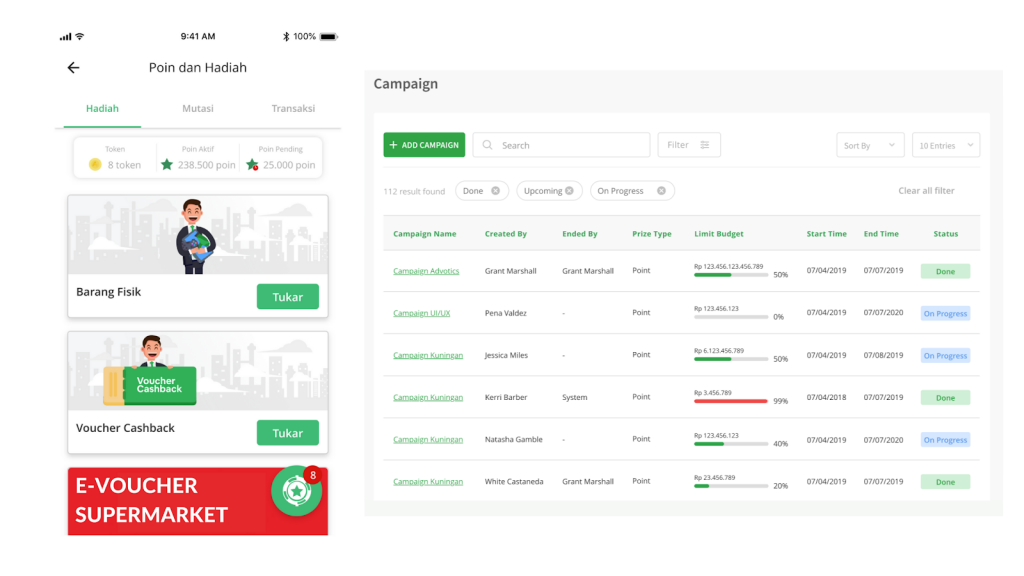
3. Reduce expenses by optimizing operational costs
Pain points:
High operational costs are often caused by less than optimal use of resources and delivery routes. For example, heavy vehicles such as forklifts, trucks, etc., are the biggest contributor to high operating costs. However, many companies often don’t know how long the duration of use of these vehicles is in the field. Is it maximized? Underutilized? Are there many unused vehicles in the warehouse?
Each vehicle is implemented with a GPS tracker integrated with the software that will collect status, location from time to time, and duration of use.
The Delivery Planning System (DPS) can automatically generate the most recommended route, according to selected parameters such as dynamic visiting hours, total working hours and driver specifications, and customer priorities.
If the vehicle carries the product, the system can also facilitate parameters such as the type of product transported, the vehicle type, capacity and specifications, order fulfillment in the correct delivery window (date and time of delivery). All information is integrated in real-time allowing last-minute schedule changes.
Benefits:
Each vehicle usage report will assist management in allocation and utilization. Maximizing vehicle productivity can reduce operating costs, the Advotics Vehicle Management System has been proven to reduce vehicle operating costs by up to 14%.
Read more:
4. Market expansion strategy
Pain points:
Before penetrating a new market, a company must perform a market analysis to validate consumer demand in the area. However, most brands fail to do a market analysis because they don’t use the right technology to do it effectively. Without accurate data and numbers, companies can only see what competitors are doing in the market, not what products are being sold and what products consumers actually buy.
Solution:
Data collected from the implementation of the QR code track and trace and loyalty program for mechanics can be accessed and analyzed in the Product Insights Analysis feature. Companies can visualize data from each SKU and run an in-depth analysis for each product performance with an objective and accurate graph because the system tracks and synchronizes all data from various data sources in real-time.
Benefits:
Analyzing the best-selling products and the prices of competitors’ products can help companies find market gaps in customer needs that competitors have not yet addressed in new areas.
Read more: What is Product Insights? Importance for Principals and Distributors?
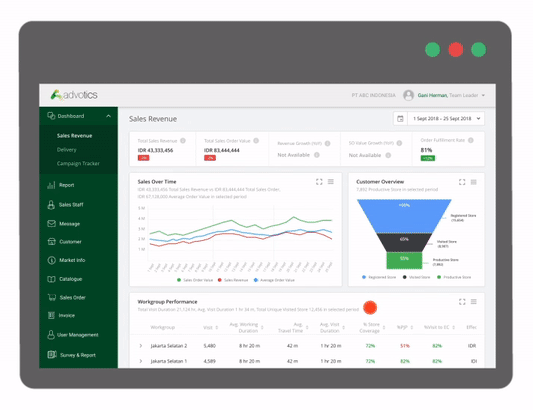