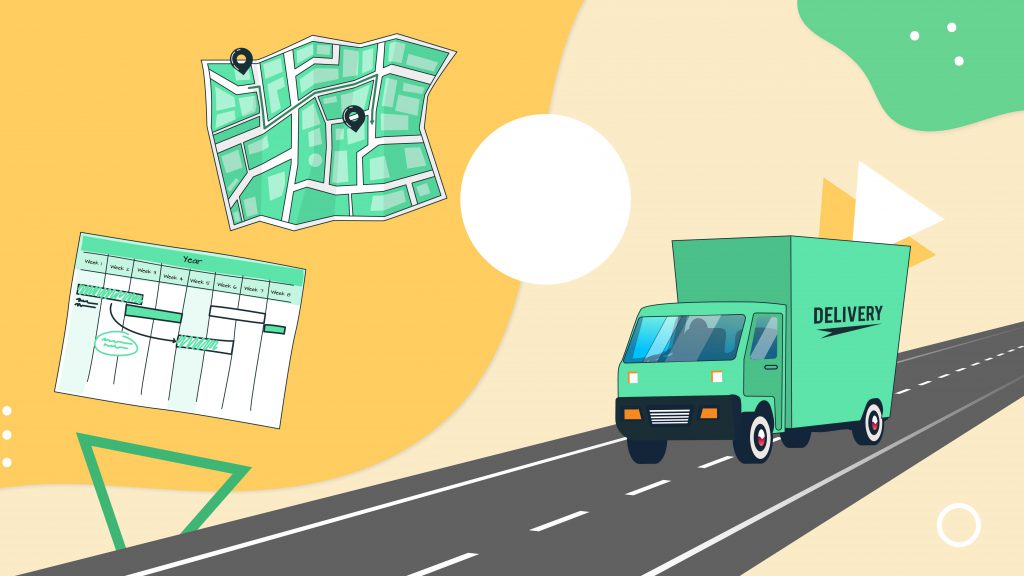
Pain Points in Routing and Scheduling for Delivery and Sales Visits
Table of Contents
A truck driver suddenly got sick? A last-minute client order has to be prioritized?
Is your route plan and delivery schedule optimal? Is there a solution that can possibly save more operational costs? Is it possible to increase the number of visits and order capacity without increasing the number of fleets?
These are some of the many pain points and concerns that distribution/logistics managers and supervisors experience on a daily basis.
Distribution managers and supervisors face several challenges that affect productivity and profitability when scheduling a route plan. If a company has hundreds, if not thousands of destinations to visit, planning routes manually quickly becomes an inefficient, expensive, and time-consuming process.
Why Should You Start Implementing a System?
It takes a lot of time and in-depth knowledge to plan a route based on vehicle capacity, number of couriers, number of customers, customer location, working hours, operating hours, and other variables. Therefore, to manage even the smallest number of fleets, a large number of shipping and operational staff are required.
As teams, sales orders, and businesses grew, manual route scheduling quickly became an impossible process. Increasing customer demand will push companies for tighter delivery windows so that optimal scheduling and automation of visit routes are increasingly important.
If the company cannot provide the best service, clients will look for another company that can. Every minute wasted each day on an unoptimized route can quickly eat away the company’s profits.
Pain Points for Scheduling a Route Plan:
1. Low Efficiency
Is the destination address already accurate? Is the company using too many vehicles? Or are there any underutilized couriers and trucks? Has the company already achieved the best route scheduling? Is the distance or travel time already optimal?
Inefficient routes can result in wasteful resource usage, which can lead to very high operational costs.
2. Time-Consuming
If the planning process is still done manual/semi-manually, with the more visit and delivery destinations to map, the higher the planning time and the more employees required. Is there any strategy to accelerate route planning time without hiring more employees?
3. Inflexible
What happens if a truck suddenly breaks down, the employee suddenly gets sick? Or an important client submitting last-minute orders? On a large scale, route planning can take hours (or even days) to readjust. If the process is inflexible, it can lead to delivery delays, canceled deliveries, and dissatisfied clients.
Advotics Route Management System (RMS)
With the right route automation system, companies can:
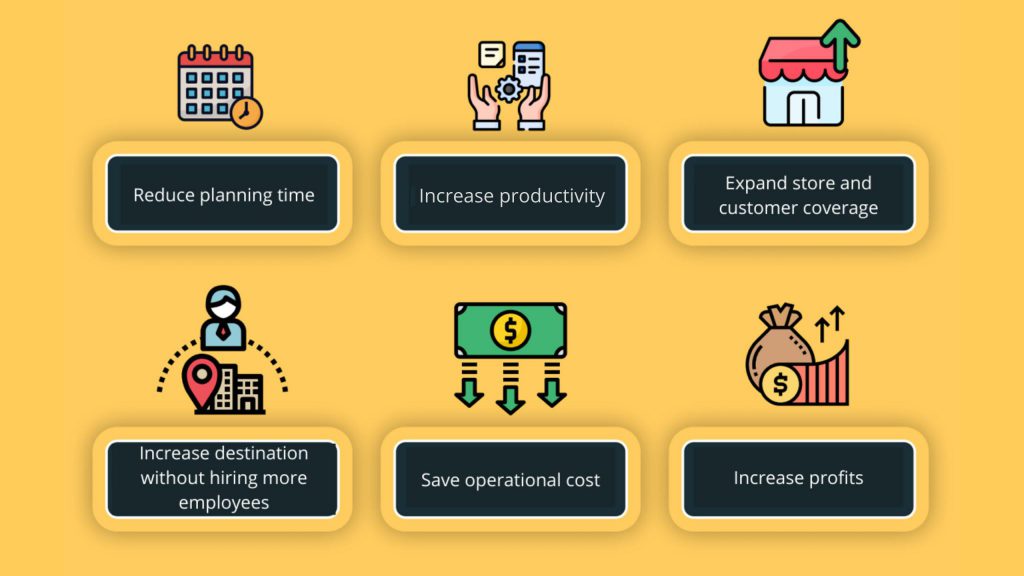
One of Advotics’ clients previously spent 1-2 days planning the monthly schedule for their thousands of field agents for the whole country. But with Advotics RMS, that process is cut down to less than an hour.
Advotics RMS automatically generates the most recommended route according to selected parameters such as dynamic visiting hours, total hours worked, customer priority, and more. All information is integrated in real-time allowing last-minute schedule changes.
Advotics Delivery Planning System (DPS)
In contrast to RMS which only focuses on sending field employees to various destinations, DPS can facilitate route planning for delivery of goods by courier and truck to several destinations at once. Why is it differentiated? Because distributing products to market adds several delivery constraints that must be facilitated, such as matching locations, types of products transported, types and specifications of vehicles, vehicle capacities, fulfilling orders within the right delivery window (date and time of delivery) as well as driver’s working hours and their driving specifications.
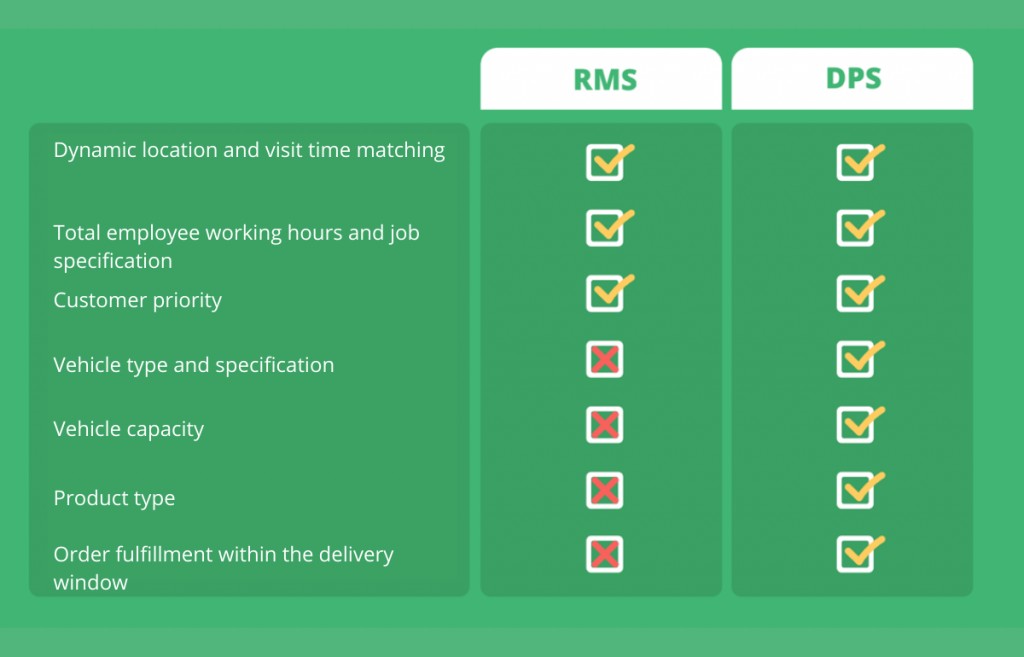